- Shop All Documents + Bundles
- FORS V7.1 Document Bundle | Bronze (15 Policies)
- Transport Manager Compliance Pack (10 Policies)
- Transport Manager Compliance Pack (6 Policies)
- Health & Safety Policy Template
- Fuel, Emissions And Air Policy Template
- Operational Security Policy Template
- Serviceability And Roadworthiness Policy Template
- Road Traffic Collision Policy Template
- Counter Terrorism Policy Template
- Load Safety Policy Template
- Vehicle Routing And Scheduling Policy Template
- Driving Standards Policy Template
- Driving Hours Policy Template
- In Cab Technology Policy Template
- Passenger Safety Policy Template
- Complaints And Grievances Policy Template
- Drug And Alcohol Management Policy Template
- Hazard And Risk Identification Policy Template
- VOR (Vehicle Off Road) Policy Template
- Tyre + Wheel Policy Template
- Health & Eyesight Policy Template
- Transport Infringement Policy Template
- Walk Around Check (Defect Check) Tool Box Talk Template
- Transport Manager CV Template
- Social Media Policy Template
- Transport Manager Contract Template
- External Transport Manager Contract Template
- Driver Handbook
Five-point plan for maximising forklift uptime
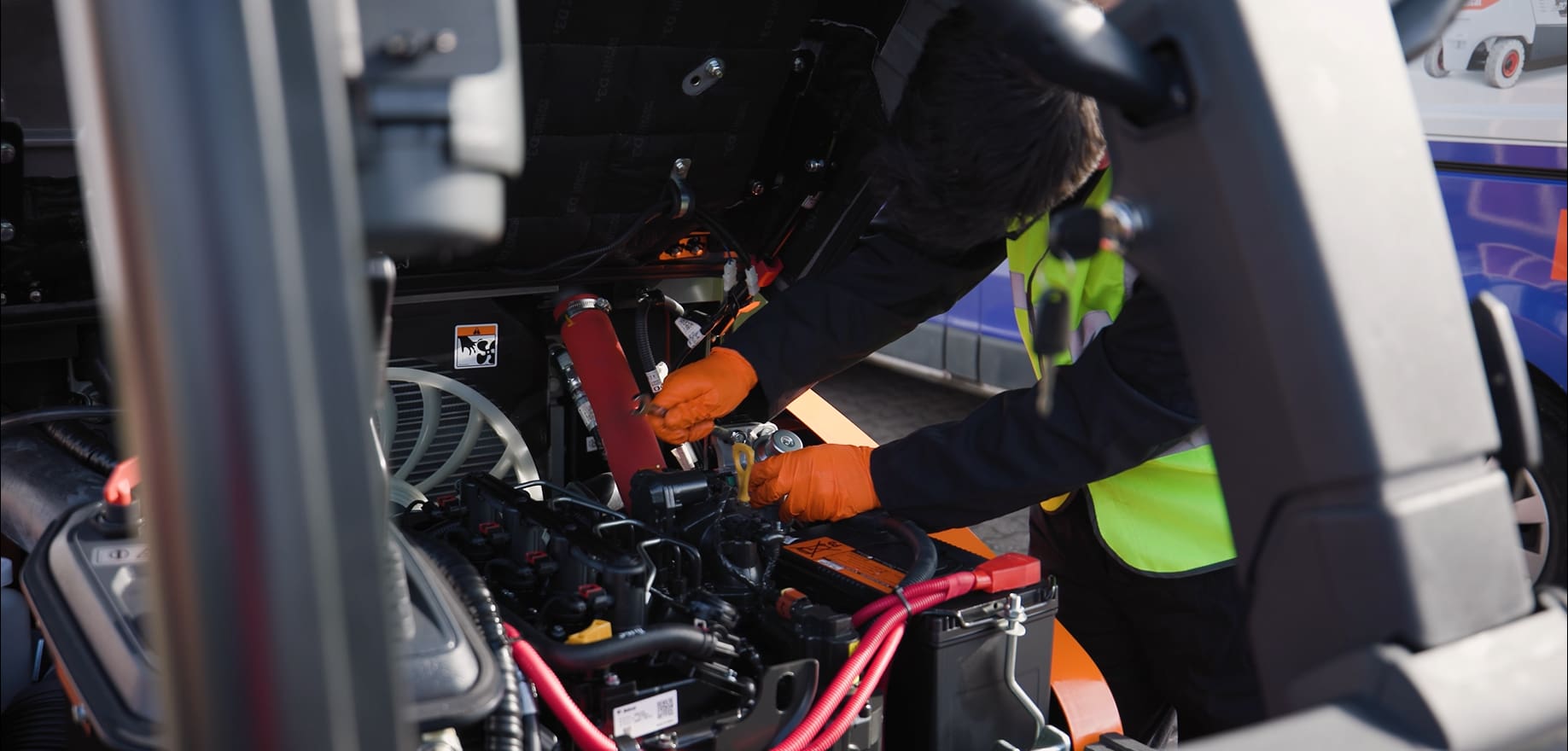
Five-point plan for maximising forklift uptime
What are the benefits from regular forklift truck maintenance and servicing? Steve Briscall, National Training Manager and Sam Cook, Technical Training Manager, at Rushlift offer a five-point plan for uplifting fleet performance
A vast number of businesses are critically dependent on the smooth running of their forklift truck fleet. Any downtime may have a huge impact on production, on-site handling or vehicle loading and may cause delays, customer disappointment and ultimately in some instances, significant financial losses.
Ensuring maximum uptime across the fleet takes planning and regular servicing, so that only the most appropriate vehicles are specified for the task and maintained for peak, safe performance.
And yet, how well planned, maintained and managed is the average fleet? How sophisticated is the analysis of vehicle usage data – is utilisation evenly spread across the fleet? What are the damage trends and causes? And is servicing being regularly carried out?
Monitoring every aspect of the fleet should be an on-going process, controlled and managed by specialists that understand the importance of regular servicing, damage control, compliance issues and cost analysis.
Here’s a five-point plan for top fleet performance:
1. Compliance
As a matter of legal compliance, businesses are required to carry out a full service on an industrial vehicle at least once a year under PUWER (Provision and Use of Work Equipment Regulations 1998). In addition, if the truck lifts a load above 300mm then it must also have a ‘Thorough Examination’ LOLER (Lifting Operations and Lifting Equipment Regulations) inspection every 12 months, as well. But legal compliance is just the bare minimum requirement.
There is a long list of reasons why it pays to follow a rigorous schedule of regular servicing, carried out by a competent, qualified maintenance engineer.
2. Enhanced safety
First and foremost, well maintained trucks are inherently safer, reducing risk of injury to operators and protecting the well-being of personnel on site. Being diligent on maintenance, with regular servicing, is an important contributor to the safety culture of the business and demonstrates the healthy attitude of management to following health and safety guidelines – which helps mitigate risk to directors in legal cases relating to industrial accidents and claims of negligence.
Regular chain-wear inspection and maintenance, along with service checks on tyre condition, brakes, axles, fork-wear, wheel bearings and greasing are critically important. These checks should be carried out monthly or perhaps, more frequently if a truck is working in particularly harsh conditions – such as rough uneven surfaces, dusty or corrosive environments.
3. Reliability and performance
With regular maintenance and servicing a vehicle will experience less downtime, making a truck far more productive in its operational life and reducing the likelihood of a catastrophic failure – avoiding all the costs of an emergency call-out and loss in productivity. What’s more, regular servicing extends the life of the truck too, resulting in greater value delivered over the whole life cycle of the vehicle. Importantly, regular servicing helps identify small problems that could become bigger problems if left, so making an early fix can be a lot cheaper, and less impactful on the business than if you leave it.
4. Records and analysis
Keeping a thorough and complete record of service history, parts and replacements, relating to each vehicle in the fleet is an essential asset to the business, not just for charting the performance of the vehicle, but for keeping track of costs and as a record of good service history, should it be needed. A comprehensive service management system capable of scheduling, recording actions, parts used and readily available 24/7 to service engineers, and management, is a valuable tool that may offer detailed analysis on each truck’s performance across the site or sites.
Rushlift’s proprietary Fleet Management System is an online platform that enables customers to access up-to-the-moment information on a forklift truck fleet, log breakdowns on a 24/7 basis and access maintenance records, account details and other vital information. Importantly, live data is fed through the engineer’s tablet making site visits simpler, with all maintenance records updated in real-time.
5. Vital support
Businesses competing on tight delivery windows or critical production schedules will need the reassurance of a reliable service support network. Rushlift has service centres located strategically across the UK and over 90 highly qualified field service engineers on the road at any one time, enabling the company to provide an engineer on site within 4 hours (average response time to VOR KPI).
Of course, fast and easy access to parts is a fundamental support function – waiting for parts to arrive from a distant European parts store can cause delay and increase down time. Rushlift’s UK Parts Distribution Centre carries in excess of £1 million worth of stock for next-day delivery. With a 4.00pm cut-off for orders – one of the latest in the industry – customers get the best possible support, all from within the UK.
At Rushlift, we work closely with the fleet owner over the entire length of the contract to maximise the overall performance of the fleet: from specifying and recommending the most appropriate trucks for the duties to be performed – and that means providing the best truck for the job, whatever the make – to providing full, regular servicing, fast breakdown call-out, and on-site meetings to review fleet performance. From analysing the usage of individual trucks Rushlift experts can make recommendations that may save significant costs, whilst improving operational performance and reliability – maximising asset value across the life-time of the fleet.

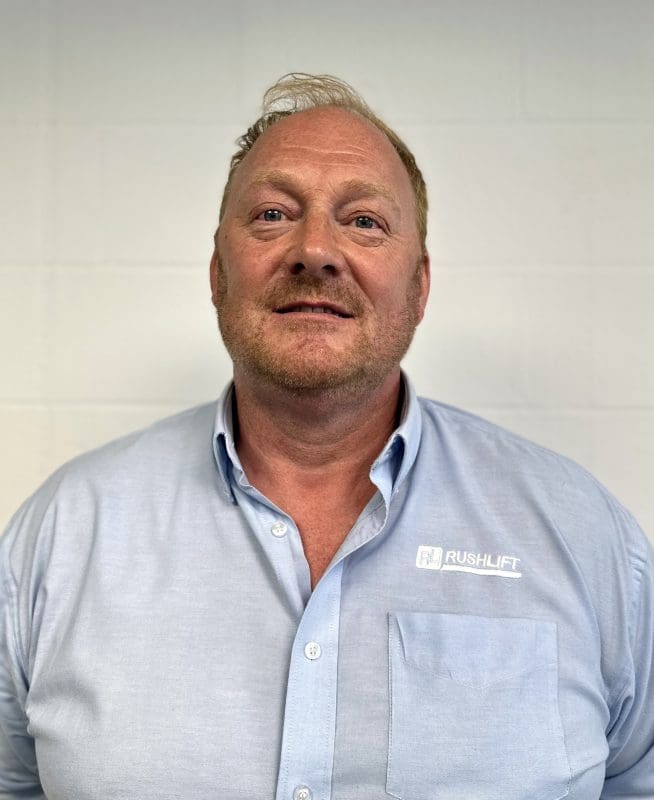
