- Shop All Documents + Bundles
- FORS V7.1 Document Bundle | Bronze (15 Policies)
- Transport Manager Compliance Pack (10 Policies)
- Transport Manager Compliance Pack (6 Policies)
- Health & Safety Policy Template
- Fuel, Emissions And Air Policy Template
- Operational Security Policy Template
- Serviceability And Roadworthiness Policy Template
- Road Traffic Collision Policy Template
- Counter Terrorism Policy Template
- Load Safety Policy Template
- Vehicle Routing And Scheduling Policy Template
- Driving Standards Policy Template
- Driving Hours Policy Template
- In Cab Technology Policy Template
- Passenger Safety Policy Template
- Complaints And Grievances Policy Template
- Drug And Alcohol Management Policy Template
- Hazard And Risk Identification Policy Template
- VOR (Vehicle Off Road) Policy Template
- Tyre + Wheel Policy Template
- Health & Eyesight Policy Template
- Transport Infringement Policy Template
- Walk Around Check (Defect Check) Tool Box Talk Template
- Transport Manager CV Template
- Social Media Policy Template
- Transport Manager Contract Template
- External Transport Manager Contract Template
- Driver Handbook
Manufacturers are leading the way to adopt automated handling technology
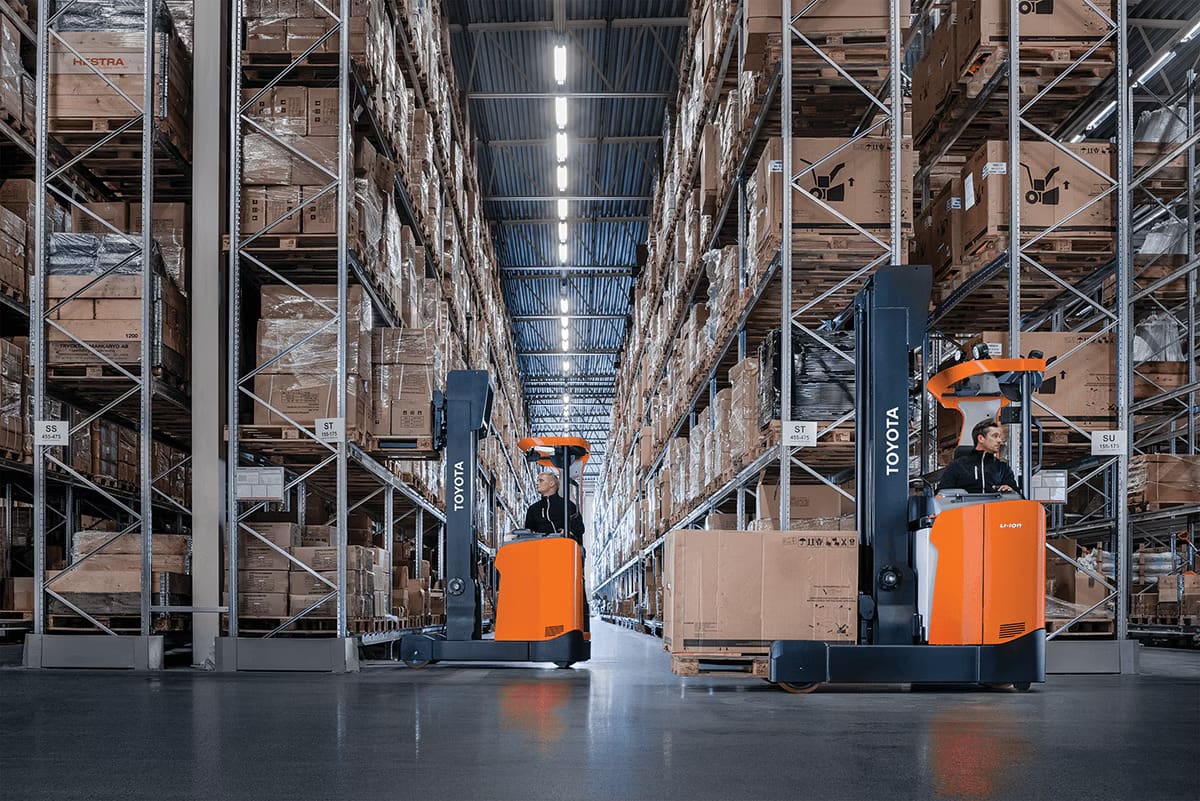
With the emergence of increasingly flexible and scalable solutions, more and more manufacturers are choosing to automate their intralogistics processes
There may be no official numbers or industry stats to back-up the theory, but manufacturing companies have always appeared to embrace automated handling and storage technology more willingly than businesses operating in other industry sectors.
Perhaps manufacturing companies view the adoption of automated storage and handling solutions as a natural progression within their business because so many of the processes undertaken within a modern production unit have been highly automated for a long time.
Historically, investing in automated storage and materials handling required something of a leap of faith – and a large budget. This was thanks in part to the fact that installing the technology usually meant that the entire warehouse process had to be automated.
But that is no longer the case. With product developments leading to the emergence of increasingly flexible and scalable solutions, it is possible to automate only those aspects of the warehouse or factory’s handling and storage process that have most to gain from moving away from manual handling methods.
Significantly, this has opened the possibility of introducing automated handling technology for many companies for whom such advanced solutions would previously have been financially out of reach.
For example, many SME manufacturing firms are opting to introduce automated guided vehicles (AGV’s) as a means of mitigating the impact of the nationwide shortage of skilled forklift operators on their business.
AGV’s – such as Toyota’s Autopilot series – offer several benefits in addition to delivering lower labour costs, including reductions in inventory and building infrastructure damage as well as increased productivity. These notable advantages bring a rapid return on investment.
And yet, despite its myriad benefits, automation is not the answer for everyone. Each manufacturer’s intralogistics flow is different and what works for one business may not be appropriate for another.
So, is automation suitable for your operation? As a starting point, consider the following questions in relation to your facility:
– Are warehouse-driven delays a common issue?
– Do everyday workflows include a vast amount of manual, repetitive tasks?
– Is output directly affected by limitations within the workforce?
– Are inventory counts regularly affected by inaccuracies?
If you answer ‘yes’ to any of these questions your business will almost certainly benefit from the operational gains that today’s highly cost-efficient automated systems offer. So, if automated storage and handling solutions aren’t already on your radar it’s about time they were!
Toyota Material Handling has successfully delivered hundreds of automated projects to manufacturers across Europe. By applying a systematic approach to identify a client’s most common storage and handling functions, we design systems that fit a client’s needs and drive productivity, increase efficiency and lower costs.